作業工程
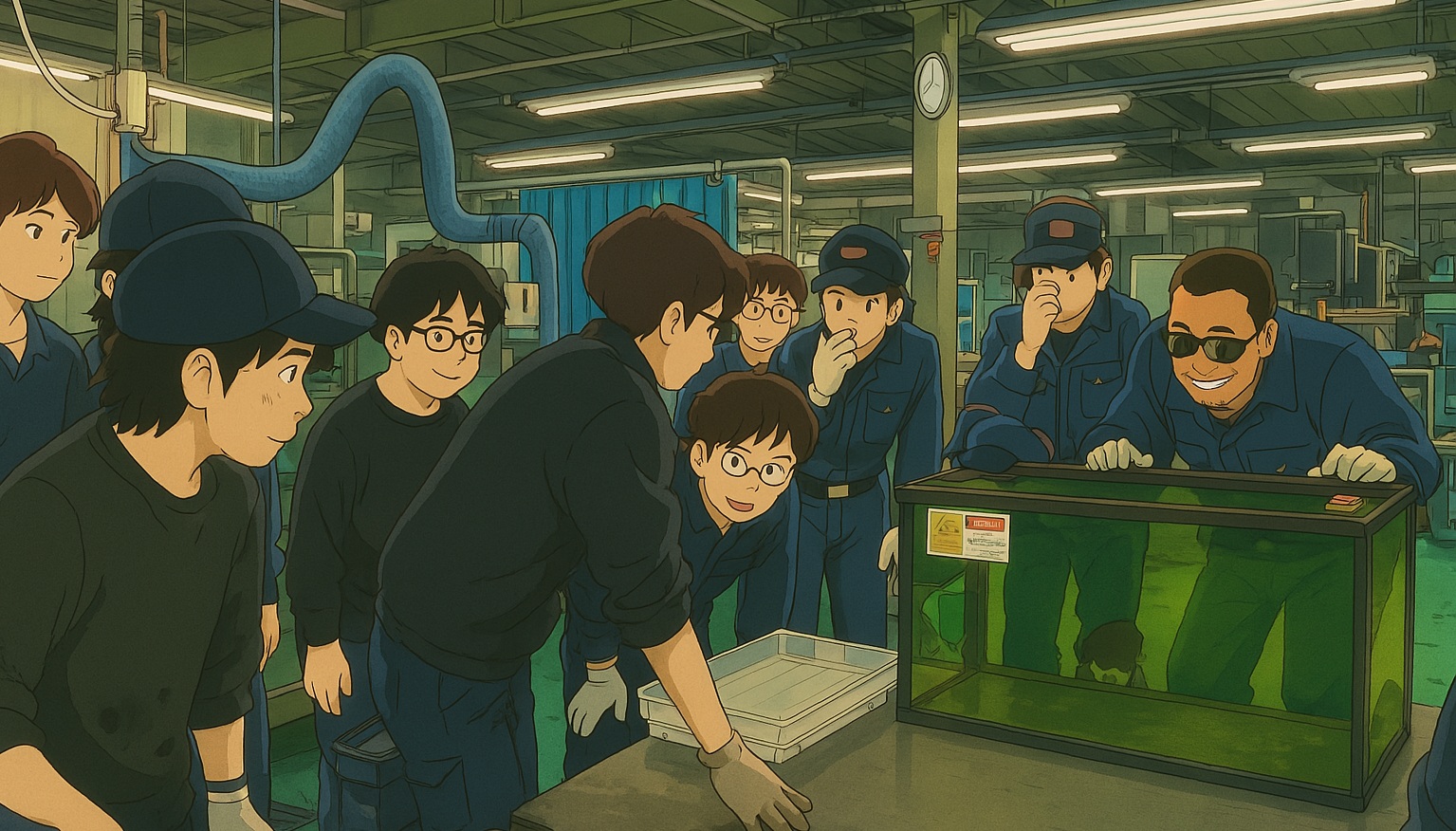
01
事前協議(お見積り)
お問い合わせ後に、当社に、メール及び郵送で図面提供をしていただきます。図面提供後、製作に入る前に、材料、板厚等などを精査して お客様と十分に協議いたします。この際に、当社の、スタッフから必要であれば材料の選定、加工方法等やVA・VGによるご提案もさせていただきます。この協議に納得の上、プログラム作業に入らせていただきます。一元化生産管理体制をとっておりますので、ここでの協議内容も製作指示書に反映していきます。
02
プログラム行程
2D、3Dでのプログラム作業に入りますが、ただ図面通りにプログラムを作っていくのではなく、材料・板厚・加工方法を考慮しあらゆる方向から解析していきながら、プログラムしていきます。
図面上では気づかないような点も、3D上で解析することで、見えてくるものがあります。当社のプログラマーは解析能力にも優れているため製品になる前にリスクを提案でき、お客様に無駄な時間を与えません。当社のプログラマーと納得いくまで打ち合わせをしてください。
03
試作行程
新商品開発には試作が不可欠になる場合があるため、当社では、お客様の試作ご要望以外にもこちらから試作品の提案をさせていただく場合があります。これは、形にしてみて初めて分かる不具合等を早期に発見して量産・組み付けに入ってからの作業効率化など、お客様のリスクを低減するための重要な工程となります。
04
ネスティング
この作業では、歩留まり、板材の効率的な割り付けをして、いかに材料を無駄にしないか、いかに効率よく作業ができるかなど、すべてを段取りしていく重要な工程のため、高度なスキルを持った技術員が担当いたします。
05
ブランク
トルンプ製レーザー複合機を使い、複雑な形状なども綺麗に短時間で作業することが可能です。
06
エッジ取り・タップ加工
ここでは、ブランク工程後にバリが発生した場合のバリを除去していく工程です。ここでは平板の状態なのでバリを完全に除去して後工程に流します。バリの除去ができていないと装置が組み付かない、食品関係等のお客様の場合には装置の清掃中にバリがあると怪我をしてしまうという重大な事態になります。そのため、特に厳しい目をもった技術員を配置しています。
07
曲げ加工
当社、独自の冶具を使いながら特殊形状加工にも対応しています。1度ご相談ください。
08
溶接工程
金属の材料・板厚に最適な溶接方法でTruDisk3001・YAGレーザーなどを使い高度な溶接を短時間で、綺麗な溶接が可能となります。この溶接の美しさが次工程の仕上げ作業の時間短縮にもなります。なお、薄板同士の溶接も可能ですのでご相談ください。
09
表面処理
仕上げ作業
協力企業による、塗装・各メッキ・印刷・彫刻の表面処理にも対応しております。
10
検査
最終出荷
検査工程では、寸法検査・表面処理検査を専用の機器を使いお客様の検査基準、当社の検査基準をクリアした製品を出荷工程に送り、衝撃に強い専用の梱包材・梱包方法を使いキズのない状態でお客様のもとに納品しております。発送は、日本全国対応しております。